LFP powder sieving machine
What is LFP powder sieving machine?
LFP powder sieving machine is a device specially used for grading and screening of lithium iron phosphate powder materials, and is widely used in the production process of raw materials for new energy batteries. As a battery cathode material, LFP requires high purity and uniform distribution to ensure battery performance. Screening machines can be configured with single or multi-layer screens to achieve multi-level screening. Through vibration classification technology, LFP powder is separated by particle size. The commonly used screening mesh is 100-400 mesh (about 150-38 microns) to significantly remove oversized particles or subdivided particles.The equipment supports high-capacity operation, and the single-unit capacity can reach 1-3 tons/hour, meeting the needs of large-scale continuous production.
The main function of LFP powder sieving machine
LFP powder sieving machine is used to accurately grade lithium iron phosphate powder, remove impurities, regulate particle size distribution, and ensure material consistency and process stability. The specific functions are as follows:
Particle size classification: Through high-precision screens (commonly used screening meshes are 200-500 mesh, about 38-150 microns), LFP powder is classified by particle size, and large particles or agglomerates with unqualified particle size are effectively removed to ensure uniform distribution of powder particle size and meet the technical requirements of battery materials.
Remove impurities: Large particles, foreign matter or agglomerates generated during the production process that may exist in LFP powder to ensure the purity of the powder. During the screening process, foreign matter such as metal chips, fibers, and agglomerates mixed in during the production process can be removed to improve the purity of LFP powder and reduce the impact on battery performance.
Control particle size: According to the production process requirements, LFP powder is graded according to different particle sizes to obtain powder that meets specific particle size requirements. Screening helps to disperse agglomerated powder, improve the fluidity of powder, and facilitate subsequent mixing, coating and other processes.
What is the working principle of the LFP powder sieving machine?
LFP powder sieving machine uses a vibrating screen to separate lithium iron phosphate powder according to particle size, sieve fine materials, and retain coarse materials to achieve particle size separation. The following is its specific working principle:
LFP powder is evenly distributed to the sieve surface through the feed port.
The sieving machine uses a driving device such as a vibration motor, an eccentric wheel or an airflow to make the sieve surface produce a specific movement . This causes the sifter to disperse and flip on the sieve surface. The particles in the sieve holes are screened and graded according to the designed size. Particles smaller than the sieve holes fall through the sieve holes into the lower layer or the collection device, which is called the undersize; particles larger than the sieve holes remain in the sieve holes, which is called the oversize.
Stocks of different particle sizes are notified through their respective discharge ports to complete the classification.
What are the advantages of LFP powder sieving machine?
The common advantage of LFP powder sieving machine is that it can well solve the problems of LFP powder bridging blockage, LFP powder loss, unstable conveying efficiency, and LFP powder particle agglomeration and poor fluidity:
Solve the problem of LFP powder bridging and clogging: The particle characteristics of LFP powder (such as uneven distribution or humidity influence) are prone to form mixing arches or sticky material arches, resulting in pipeline blockage. LFP powder sieving machines are usually equipped with vibration devices, which destroy material arches through high-frequency vibration or probe action to promote the flow of LFP powder. The sifter adopts a fine screen design, which can effectively separate large pieces of inventory or foreign matter.
Solve the problem of LFP powder loss: The sifter has a relatively gentle effect on the material during operation, does not generate excessive mechanical stress and heat, reduces the mixing of debris caused by equipment wear into the material, and thus reduces material loss. The efficient screening capability can accurately control the particle size range, ensure the uniformity of the material particle size, and avoid the loss of some LFP powder materials due to uneven particle size.
Solve the problem of unstable conveying efficiency: By accurately controlling the vibration frequency and amplitude, the LFP powder sieving machine can stabilize the target particle size particle pass rate at a high level, ensuring the stability of the screening efficiency. The screening machine has a high degree of automation, and can achieve manual operation without manual operation with the automatic feeding and receiving system. It can operate continuously for 24 hours, reducing the uncertainty and error caused by manual operation.
Deal with the problem of LFP powder particle agglomeration and poor fluidity: LFP powder is easy to absorb moisture or agglomerate due to static electricity, resulting in conveying blockage and uneven feeding, affecting the uniformity of subsequent processes (such as coating and mixing). The powder screening machine destroys the agglomerates through high-frequency vibration or ultrasonic vibration devices, restores the fluidity of the powder, and reduces the agglomeration caused by mechanical extrusion.
Recommended mesh size for LFP powder sieving machine
LFP powder sieving machine is suitable for material screening processing with different mesh sizes: coarse screening (100-150 mesh) for impurity removal, medium screening (150-250 mesh) for balanced efficiency, fine screening (250-400 mesh) for purification, and ultrafine screening (>400 mesh) to meet high-end needs.
100-150 mesh (about 150-100 microns): suitable for coarse screening, used to remove large particle impurities, agglomerates or incompletely crushed materials, increase particles or clusters, often used in the rough processing stage of LFP powder to ensure that the raw materials basically meet the particle size requirements.
150-250 mesh (about 100-63 microns): suitable for intermediate pore size, balance uniform pore size and production efficiency, widely used in intermediate pores in the preparation of battery cathode materials.
250-400 mesh (about 63-38 microns): recommended for fine screening to meet the requirements of high-performance batteries for fine particles and ultra-high purity, especially in the production of high-end power batteries.
Ultrafine screening (>400 mesh or <38 microns): If the particle size requirements for LFP powder are extremely high, such as for some high-end battery products or special application scenarios, finer screens may be used, such as 400 mesh or even finer. For special needs (such as 2-10 micron particle size), high-precision classifiers can be used, which are suitable for laboratory or ultra-high precision applications.
Application of LFP powder sieving machine
LFP powder sieving machine runs through the entire production process: raw material pretreatment, classification after synthesis, screening before slurry preparation and recycling and reuse, ensuring particle size uniformity and improving battery performance and safety.
Wholesale of raw materials in LFP powder production
Before LFP powder synthesis, raw materials (such as phosphate, iron salt and lithium salt) are ground into fine particles and sieved to ensure the uniformity of subsequent reactions. The sieving machine uses a vibrating screen to grade the particle size of the ground raw materials and screen out oversized or undersized raw material particles. For example, 10-50 micron particles are screened out for synthesis. Through screening, the uniformity of raw material particles is improved, the formation of clusters during the synthesis process is reduced, and the crystal structure consistency of LFP powder is improved.
Grading treatment after LFP powder synthesis
After LFP powder is synthesized by high-temperature solid phase method or process, the particle size distribution is wide (such as 1-100 microns), and the specific particle size requirements for array manufacturing need to be adjusted. LFP powder sieving machine uses a plasma sieving machine to finely screen the synthesized LFP powder, separate the powder in the target particle size range, and enhance agglomeration and adjustment at the same time. The powder distribution after screening is sparse, which improves the dispersion and consistency of the battery slurry, thereby improving the battery capacity and cycle performance.
Powder screening before battery slurry preparation
On the battery production line, LFP powder needs to be mixed with conductive agent and buffer to prepare slurry. To avoid nozzle etching or uneven casting, the powder needs to be strictly screened. LFP powder sieving machine uses an aperture screener (such as an airflow screen or a graded vibrating screen) to remove particles with larger apertures (such as 20 microns) and temporarily stop. Screening improves the fluidity and stability of the slurry, reduces electrode surface defects, and improves the consistency and safety of the battery.
LFP powder recovery and reuse
In the process of waste lithium batteries, LFP powder can be extracted by physical or chemical methods, but the recovery powder often needs to be restored to the damaged or uneven particle size, and needs to be redistributed before it can be reused. The screening machine uses a multi-stage vibrating screen or a centrifugal screener to wash and screen the recovered LFP powder, separate the reusable powder and remove the residual carbon material or metal particles. Screening improves the distribution and availability of recycled powder, reduces the cost of secondary utilization, and promotes the circular economy.
LFP powder sieving machine is an indispensable key equipment in the lithium-ion battery LFP positive electrode material industry chain. Its application runs through all aspects of LFP powder production, processing, and recycling. It is of great significance to ensure battery performance, improve production efficiency, and promote the development of the battery recycling industry.
-
Granules, powders, and paddle materials can be used.
-
Meet the needs of large-scale and high-precision screening
-
Pharmaceutical excipient powder vibrating screen
Pharmaceutical excipient powder vibrating screen is a screening device designed to meet the special physical and chemical properties of...
-
TPU Polymer Powder Sieving Machine
TPU polymer powder sieving machine is a mechanical equipment specially used for particle size classification, impurity removal or particle...
-
Tea seed grading linear vibrating screen
The tea seed grading linear vibrating screen is a key equipment used in the tea processing field for screening and grading tea seeds. Its core function is to achieve...
-
EAA polymer powder sieving machine
EAA polymer powder sieving machine is an automated equipment designed for high-precision sorting, ensuring that the EAA polymer powder has uniform particle size....
-
Glutinous rice ball coating machine
Glutinous rice ball coating machine is designed for all kinds of quick-frozen glutinous rice ball, aiming to achieve efficient and uniform powder adhesion. The equipment....
-
How much is an abrasive automatic sieving machine?
Abrasive automatic sieving machine is a commonly used industrial powder sieving equipment,The price of the abrasive automatic sieving machine varies according to factors such as production capacity and technology...
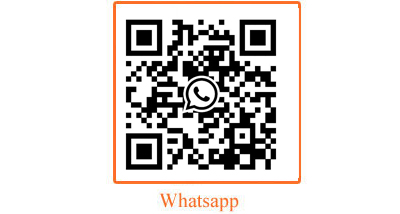
Email:
sale@xxdahan.com
WhatsApp:
+86 15236742901
Add:
1000m West of Forest Park,Yanjin County,Xinxiang City,Henan Procince,China.