EAA Polymer Powder Sieving Machine
EAA polymer powder sieving machine is an automated equipment designed for high-precision sorting, ensuring that the EAA polymer powder has uniform particle size and is free of impurities. It is suitable for the fields of electronics, medicine and special materials. The equipment adopts a multi-layer vibrating screen structure to achieve multi-level sorting, improve the screening efficiency by more than 30%, and the screening mesh range covers 80-800 mesh, which can accurately adapt to the EAA powder classification with different particle size requirements. The sieve body is made of 304 stainless steel and equipped with a food-grade silicone sealing ring to ensure that the material is contaminated.
EAA polymer powder sieving machine video
What is the working principle of EAA polymer powder sieving machine?
The working principle of the EAA polymer powder sieving machine is mainly to use the exciting force generated by the vibration motor to make the sieve machine produce a compound rotation and compound motion, driving the screen to vibrate at a high frequency. When the EAA polymer powder enters the sieving machine:
① Material dispersion: Vibration makes the polymer powder entering the screen surface quickly dispersed, reducing the agglomeration of the material and creating favorable conditions for subsequent screening.
② Separation through the mesh: Under the action of the vibration force, the fine powder smaller than the mesh aperture overcomes a certain resistance and falls through the mesh aperture to the lower layer, becoming the sieve undersize.
③ Discharge of the sieve: Coarse powder or impurities larger than the mesh aperture cannot pass through the mesh aperture. Under the continuous vibration of the screen surface and the continuous feeding of materials, they move along a certain trajectory and are finally discharged from a specific discharge port, becoming the sieve oversize.
By selecting sieves with different mesh sizes, the particle size range of the EAA polymer powder finally separated can be controlled. The screening efficiency and accuracy are affected by many factors such as vibration frequency, amplitude, mesh structure, and material characteristics.
What are the disadvantages of the EAA polymer powder sieving machine?
Loss of EAA polymer powder particles: During the screening of fine powder, due to the small aperture of the screen, powder particles are more likely to be lost due to vibration during screening, resulting in a decrease in the output of finished products. Use a preliminary screen with a larger aperture for coarse screening to reduce excessive loss of particles, and then perform fine screening.
Static electricity accumulation problem: EAA powder is prone to static electricity due to friction during the screening process, which will cause powder particles to accumulate on the surface of the screen and affect the screening effect. You can choose a screening machine with anti-static function or ground the equipment to reduce the accumulation of static electricity.
Noise and vibration problem: When the screening machine is working, it may generate a lot of noise due to the high vibration frequency. Choose a low-noise, stable EAA polymer powder sieving machine, such as using a vibration isolation system and noise reduction design to reduce the impact of noise.
The contradiction between screening accuracy and output: When the screening accuracy is improved (such as screening above 200 mesh), the output usually decreases, because the aperture of the screen with a smaller mesh is limited, and the speed of powder passing through slows down, resulting in a decrease in output. Choose a screening machine with a multi-layer screen design to separate the coarse powder from the fine powder for multiple screenings to avoid screening too much powder at one time.
Recommended mesh number of EAA polymer powder sieving machine
Basic screening (coarse screening): 80-200 mesh
Applicable scenarios: pre-screening of raw materials to remove large particles or agglomerates; preliminary classification of powders to meet conventional processing requirements such as injection molding and extrusion;
Particle size range: 180μm (80 mesh) to 74μm (200 mesh).
Fine screening (medium and high precision): 200-400 mesh
Applicable scenarios: electronic packaging materials, thin film coatings and other fields with high requirements for particle size uniformity; screening of carrier powders in pharmaceutical excipients or sustained-release preparations.
Particle size range: 74μm (200 mesh) to 38μm (400 mesh).
Ultrafine sieving (high precision/nanoscale): 400-800 mesh (customizable 1200 mesh)
Applicable scenarios: special coatings, nanocomposite material preparation; high value-added electronic paste or 3D printing powder
Particle size range: 38μm (400 mesh) to 15μm (800 mesh), customized modules can reach 5μm (1200 mesh).
The recommended sieving mesh number of EAA polymer powder sieving machine needs to be determined according to its specific application field and the required final product particle size. EAA powder is widely used, and different applications have different requirements for the fineness and uniformity of the powder.
What is the application of EAA polymer powder screening machine?
Packaging material production: EAA powder needs to have a uniform particle size to ensure coating consistency and bonding strength. The sieving machine often uses a 100-150 mesh screen to sieve out powder with a particle size of 0.1-0.15mm and remove oversized particles or agglomerates. For example, in the production of multi-layer co-extruded films, the sieved EAA powder ensures the stability of the film layer's heat sealing performance and improves the sealing of the packaging.
Cable shielding material: EAA powder is used for bonding and filling of cable shielding layers, requiring high purity and fine particle size to ensure electrical performance. The sieving mesh number recommendation of EAA polymer powder sieving machine needs to be determined according to its specific application field and the required final product particle size. EAA powder is widely used, and different applications have different requirements for the fineness and uniformity of the powder. Use a sieve of 200 mesh or more to screen out ultrafine powder with a particle size of less than 0.075mm to remove impurities and irregular particles.
Hot melt adhesive manufacturing: EAA powder is an important raw material for hot melt adhesives, and the particle size needs to be strictly controlled to ensure uniform melting and coating effect. The sieving machine is usually equipped with an 80-120 mesh screen to sieve out powder with a particle size of 0.125-0.18mm, which is suitable for scenes such as automotive interiors and textile bonding. The sieving process removes overly fine or coarse particles and improves the construction performance of the adhesive.
Powder coating: EAA powder needs to be fine and evenly distributed to ensure smooth coating and adhesion. The sieving mesh number recommendation of the EAA polymer powder sieving machine needs to be determined according to its specific application field and the required final product particle size. EAA powder is widely used, and different applications have different requirements for the fineness and uniformity of the powder. Using a 150-200 mesh screen, the powder with a particle size of 0.075-0.1mm is widely used in metal surface anti-corrosion coatings.
3D printing material preparation: In the field of additive manufacturing, EAA powder, as a 3D printing consumable, requires extremely high particle size consistency. The sieving machine uses a 250-325 mesh screen to screen out ultrafine powders with a particle size of less than 0.045mm, ensuring good powder fluidity during printing and tight interlayer bonding, which is suitable for precision parts manufacturing.
Selection suggestions
① Clarify the purpose and requirements of sieving: How much EAA powder do you need to process per hour or day? This will affect the model and size of the sieving machine you choose.
② Consider the characteristics of EAA powder: EAA powder with poor fluidity may require special vibration methods or auxiliary devices to improve sieving efficiency.
③ Choose the right type of sieving machine: According to your specific needs and the characteristics of EAA powder, common types of sieving machines include circular vibrating screens (rotary vibrating screens), linear vibrating screens, ultrasonic vibrating screens, airflow screens, etc.
④ Determine the key technical parameters:
Sieve mesh and material: Select the appropriate mesh according to the target particle size, and the mesh material should consider wear resistance and corrosion resistance.
Number of sieve layers: Select single or multi-layer sieves according to the number of particle size ranges to be separated.
Vibration frequency and amplitude: These parameters directly affect the screening efficiency and accuracy and need to be adjusted according to the material characteristics.
Equipment material: Select the appropriate equipment material, such as carbon steel or stainless steel, according to the production environment and hygiene requirements.
Inlet and outlet design: Ensure that the size and location of the inlet and outlet are convenient for connection with your production line.
⑤ Consider the maintenance and operation of the equipment.
⑥ Investigate suppliers and after-sales service
In general, EAA polymer powder sieving machine has a compact structure, simple operation, easy maintenance and cleaning. The fully enclosed design effectively prevents dust from flying and meets environmental protection requirements. The sturdy and durable material ensures the long-term stable operation of the equipment, which is an ideal choice for EAA polymer powder production and application fields. The processing capacity can reach 50-200 kg per hour, and the specific output depends on the material characteristics and sieve mesh.
-
Potato Starch Vibrating Screen
Granules, powders, and paddle materials can be used.
-
Granules, powders, and paddle materials can be used.
-
Meet the needs of large-scale and high-precision screening
-
Centrifugal screening machine
Centrifugal screening machine is designed and produced for screening problems such as light materials...
-
Pharmaceutical excipient powder vibrating screen
Pharmaceutical excipient powder vibrating screen is a screening device designed to meet the special physical and chemical properties of...
-
TPU Polymer Powder Sieving Machine
TPU polymer powder sieving machine is a mechanical equipment specially used for particle size classification, impurity removal or particle...
-
Tea seed grading linear vibrating screen
The tea seed grading linear vibrating screen is a key equipment used in the tea processing field for screening and grading tea seeds. Its core function is to achieve...
-
Paint for filter sieve
Paint for filter sieve is a device that separates large particle impurities, lumps, inadequately dispersed pigments and fillers, crusts, and debris from paint....
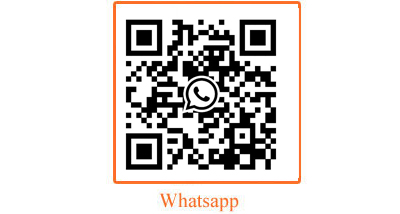
Email:
sale@xxdahan.com
WhatsApp:
+86 15236742901
Add:
1000m West of Forest Park,Yanjin County,Xinxiang City,Henan Procince,China.